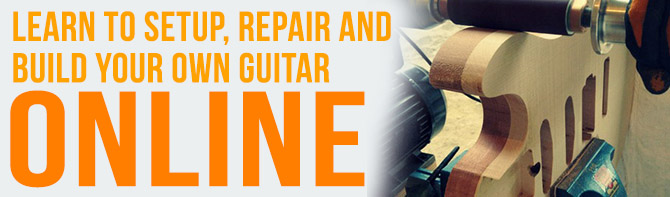
Visit the new website: www.buildyourownguitaronline.com
HOME > Different type of guitar finishing
DIFFERENT TYPE OF GUITAR FINISHING
The finishing has the effect of stiffening the external fibres of the wood, accentuating the muffle factor and increasing the frequency of resonance with respect to untreated wood.
The rule is thus: the best finishing is the one that lets the wood behave as if it has not been finished.
As a result, a unfinished instrument will always sound better than a finished one (please read
the sound of woods and the tapping method, unless the finish is very thin and very hard.
Finishing does have an important function, however, which is to protect the instrument from dirt deposits from playing it (without finishing the maple neck would immediately acquire a brown/greenish color), and from the damage that environmental changes can cause the instrument’s structure and neck stability.
When the humidity level changes, an unfinished neck (especially 'slab' cuts) would force us to make frequent adjustments to the truss rod. Instruments with the neck finished and the fretboard unfinished
(rosewood or Ebony)
also need more frequent truss rod adjustments compared to all finished maple necks.
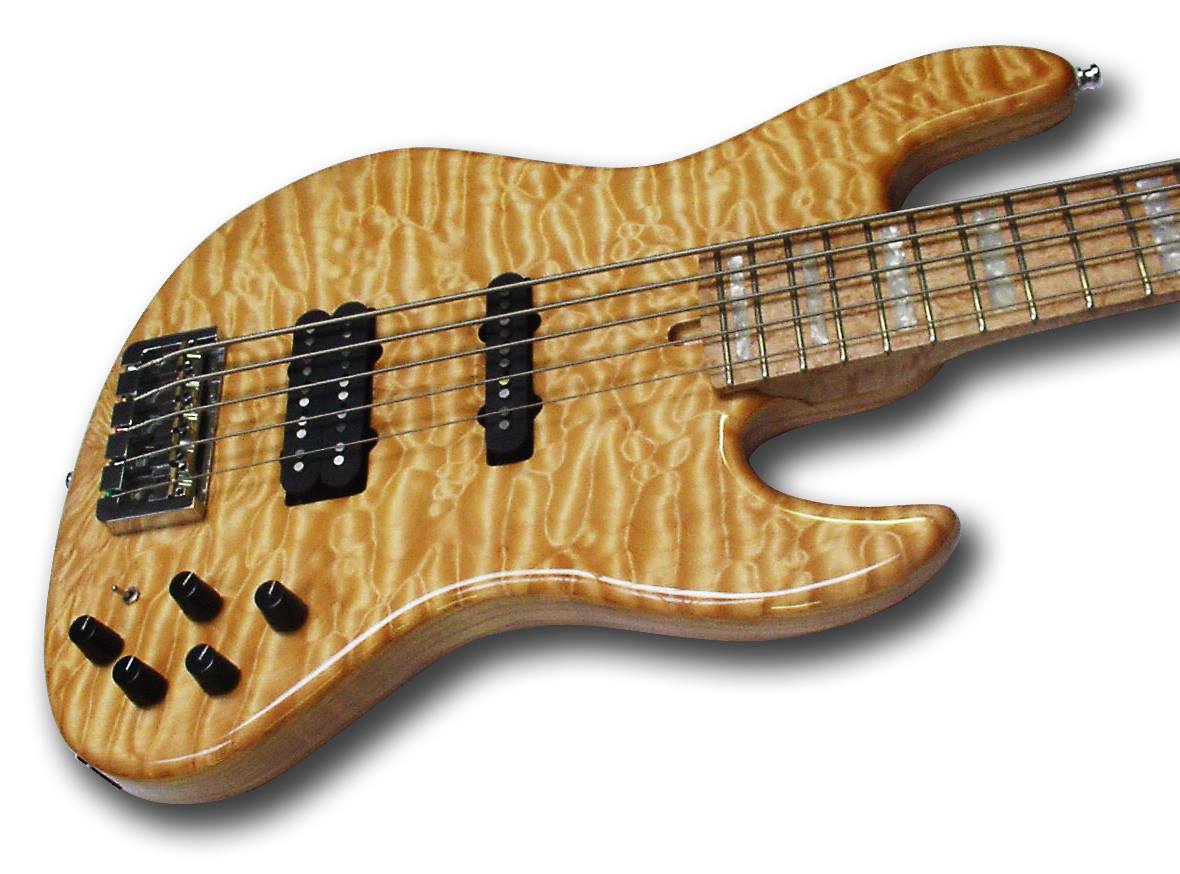
Although the impact of the finish is much greater on the soundboard (usually fir) of the acoustic instruments, it is also important in electric instruments, especially the neck.
Leaving aside the shellac finish typical of classic instruments, there are different types of treatments applicable to the electrical instrument:
Each of these will have a different impact on the way the instrument vibrates and therefore on the sound.
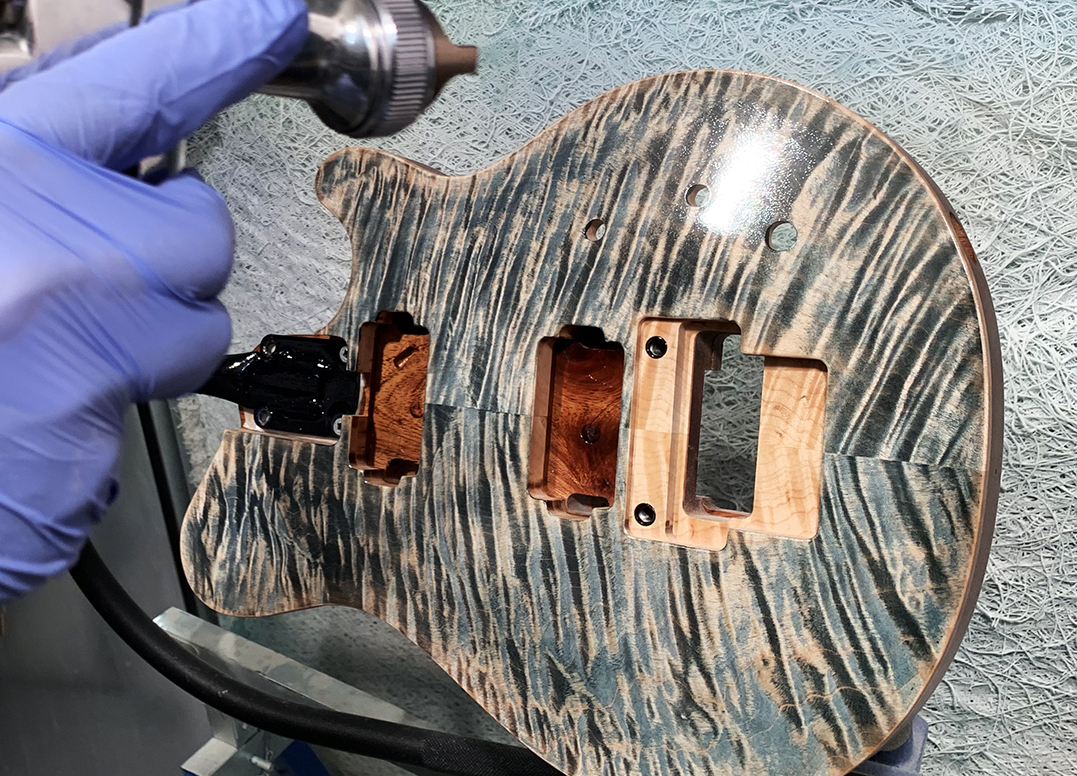
Essential oil treatments
The use of essential oils in the finishing of an instrument requires profound and long experience. This type of finish is absorbed by the wood in depth and does not dry out completely, causing a dramatic increase in the friction inside the wood especially on the neck, muffling the vibration and inhibiting high frequencies.
Oil offers only minimal protection from moisture and climatic changes and an oil-treated neck will get dirty in a short time without possibility of recovery. I don't recommend to use oils for finishing guitars at all.
Nitro finishing
Nitro is probably one of the best treatments for electrical instruments.
Over time, this type of finishing loses stickiness and dries, reducing its thickness with the double advantage of hardening (reducing the muffling factor) and thinning, thus also decreasing its influence on the sound that will become similar to that of an untreated instrument.
For this reason, the old guitars finished with nitro in the late '50s and '60s improve over the years and are sought after.
On the other hand, a nitro-finished instrument will be slightly less stable as atmospheric humidity conditions vary than a catalyzed finishing and will also be more vulnerable to mechanical shocks (scratches, impacts, etc.).
Nitro finishing is also very laborious to apply and requires very long drying times, which are not compatible with current construction times.
Polyurethane and acrylic finishing
Among the most used finishings in the field of electrical instruments are polyurethane and acrylic finishings. These are finishings made up of two components, the finishing itself and a catalyst that helps them dry.
If used properly and in minimal thicknesses, these finishings offer the best compromise between sound, resistance and protection. They dry and stabilize quickly, offering excellent protection against shocks and scratches.
Polyurethane finish may yellow over time getting a nice 'vintage' shade, while acrilics remains perfectly transparent although they are often associated to a 'plastic" look.
Polyiester finishes
Made up of finishing, catalyst and accelerator, the polyester finishing allows easy manual sanding and differs from the polyurethane and acrylic finishes for the greater filling capacity of the pore with fewer applications. Polyester finishings are mostly used on economical instruments and in scale production because of the drying speed.
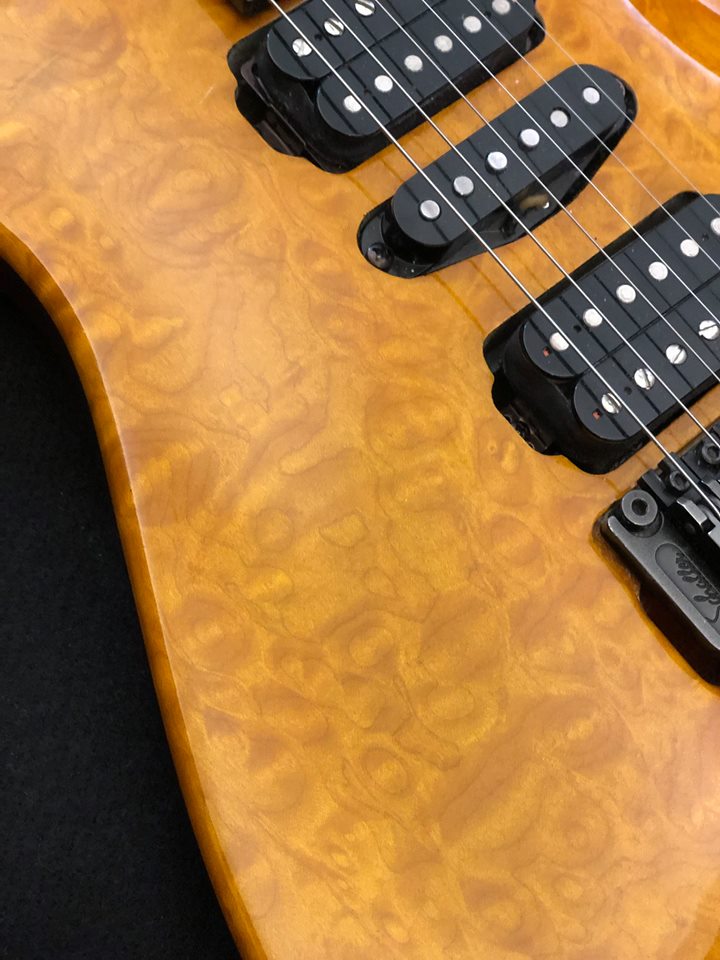
Epoxy finishing
Halfway between acrylic and polyester, epoxy finishing tend to harden more and the gloss is characterized by greater transparency and a reduced tendency to yellow.
UV finishes
These are vitrifying finishings that dry in special ovens (even small ones) thanks to the irradiation of ultraviolet rays. They correspond in character to acrylics, but drying times are immediate.
BEHAVIOUR AND AGING
You may have noticed that your instrument sounds slightly different at midday than in the evening on particularly hot days.
If it is treated with a certain thickness of finishing (as with many modern guitars), the structure of the finishing covering over the neck will change significantly over the course of the day, and this can affect the resonance of the neck and therefore cause you to hear variations in the sound.
The same phenomenon can occur during the winter when the radiators are switched on and the air becomes particularly dry.
It is therefore important to paint (but also to glue) in rooms with controlled temperature and humidity (at least 50%) to prevent the humidity from being trapped in the wood under the finishing.
The following 2010 video I made (widely cloned) demonstrates a trick to make the neck of your instrument much smoother: